Airpaq uses high-quality material and combines it with aesthetic design and practical functions to produce high-quality and extremely robust products. Each airbag is carefully opened in order to use the largest possible fabric surface. Seamstresses evaluate each fabric individually before it is dyed using an environmentally friendly process. Afterwards, laser technology is used to cut the fabrics into the desired patterns.
The seat belts, which are also received as rejects, are ready for immediate use. They become load-bearing elements of our backpacks – as back sections, shoulder straps or fasteners that combine comfort and design. Whereas the belt buckles, once part of a safety system, and which are obtained both from scrap yards and directly as rejects from security system manufacturers, become the iconic closure of the roll-top backpacks.
The founders use upcycling to manufacture their backpacks. In contrast to recycling, this concept is fundamentally more sustainable. While during recycling, the material is first sorted, washed, shredded and sometimes chemically processed, this is not the case with upcycling, where the source materials are used in exactly the same condition as they are.
The airbags used come exclusively as rejects, i.e. airbags that are new but have not passed the safety checks. This includes small “defects” such as uneven seams. Instead of throwing them away, Airpaq processes them into wearable backpacks and accessories.The products also need other materials that don’t come from the junkyard – new zippers or foam for the padding.
All backpacks, bags and bow ties with matching pocket squares are produced in a sewing factory in Timișoara, Romania, positioned close to car manufactures. Additionally, all materials are sourced from Europe. This minimizes the environmental impact of transport and guarantees compliance with strict EU environmental standards.
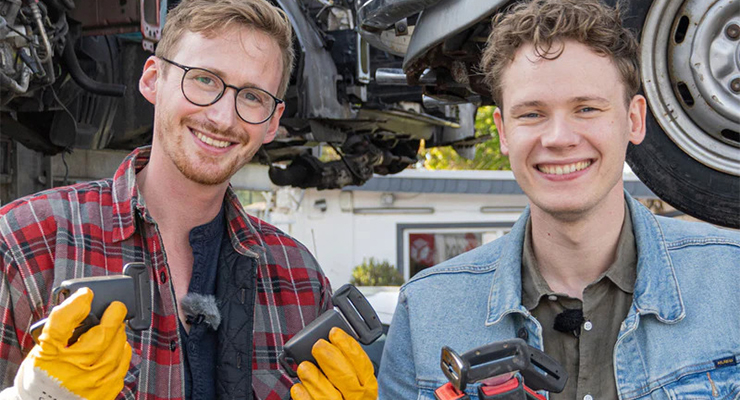